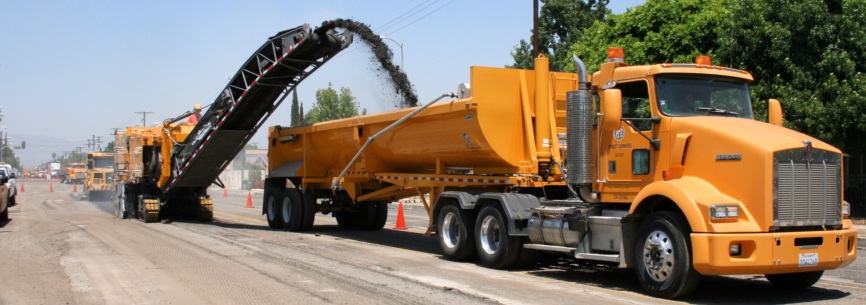
- Home
- Services
- Asphalt Roads and Surfaces
- 3D Paving & Milling Control
3D Paving & Milling Control
Synergy Service Offerings
We possess the tried and trusted technology to achieve absolute accuracy and consistency in paving and milling control. But it also comes down to operator experience and, after many years in the industry, Synergy Positioning leads the way.
Over many years in the industry, Synergy Positioning has developed paving and milling control software that delivers absolute precision; technology that is the cornerstone of our company.
We understand our clients are only interested in absolute perfection. As a result we’re used to chasing millimetres under pressure. Our 2D and 3D paving and milling control solutions have been designed to ensure the best results possible in many different environments.
When you’re chasing plus or minus 5mm across a broad reach of pavement, the process becomes as much art as science. Our team numbers several survey parties working across New Zealand and Australia 24/7 and through collaboration with our clients, they ensure milling and paving depths are consistently achieved to criteria.
Synergy Grade Control
Using our applied 2D and 3D paving and milling control technology is not only a cost effective process, but one that also provides full Synergy Positioning technical support from start to finish.
Once our client has had confirmation of the specification and design criteria of the asphalt to be laid, our team will grid survey the area to be paved.
Applications
The system comes into its own when dealing with differential compaction, where – due to varying depths within the ground gradient beneath the paved area – dips and troughs begin to form after a road roller has covered the surface.
The Synergy Grade Control System allows us to equate for any given surface’s compaction factor by giving us differential percentages to work against. While the technology we utilise provides for absolute accuracy, we also rely on the experience of our on-site Synergy Positioning teams.
After uploading the survey data, the control technology then sets the parameters for the paver’s laying depth. A Synergy Positioning operator walks alongside the machine cross-referencing this data, performing QA as we go.
This means that when our client’s road roller covers the surface afterwards, there should be no change in the level of the asphalt that has been laid. A separate QA report can then be completed by our surveyor to confirm this.
While roading projects traditionally form a large component of Synergy Positioning’s 2D and 3D paving and milling control service, we’ve also had many years experience utilising this software for clients working on airport runways, dedicated parking spaces and sports fields: all environments that demand absolute precision and smoothness of finish.
3D Paving Control
While 2D paving and milling control remains a large part of Synergy Positioning’s consultancy business, we also specialise in emerging 3D paving and milling control technology.
Where the Synergy Grade Control System requires a survey team member to load data into the paving machine on-site each time a new layer of asphalt is applied, our 3D system relies on a Robotic Total Station positioned on the milling machine; effectively giving you the equivalent of an on-site surveyor every step of the way.
This means there is less manpower requirement, potentially freeing up both time and budgetary constraints.
Additionally 3D paving control technology is useful in situations where more intricate shapes require surveying, such as intersections where a lot of cross flow data is required. The new 3D technology also provides for seamless survey mapping through obstacles such as traffic islands or manhole covers.
Services Downloads Section
Millimeter GPS Product Line Asphalt Dulles
See how Lane Construction made fast work of building taxiways at Washington DC’s Dulles International Airport using Topcon’s Millimeter GPS paving systems.
Topcon mmGPS Milling
Tayco Paving mmGPS Milling - Port Hardy Airport.
Topcon mmGPS Milling
Topcon mmGPS system in action on a Milling machine at Newark Airport.
Related Case Studies
-
Millimeter GPS Product Line Asphalt Dulles
See how Lane Construction made fast work of building taxiways at Washington DC’s Dulles International Airport using Topcon’s Millimeter GPS paving systems....
Read More