About Us
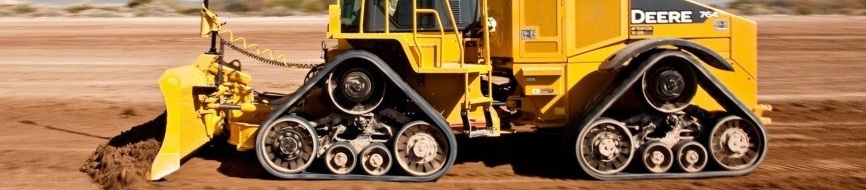
- Home
- About Us
- Case Studies
- Machine Control Technology
- Why the construction industry needs machine control
Why the construction industry needs machine control
Advanced machine control technology is already providing many Kiwi construction companies with the ability to save both time and money. Here’s how it could benefit you too.
Fast and accurate machine control technology is revolutionising civil earthworks and infrastructure project work for many New Zealand entities.
Through advanced modelling, it allows dozer, grader and excavator operators the ability to see where they are on any site in real-time.
Still not sure if the system is right for your operation? Here are five reasons why considering machine control for your fleet could prove one of the smartest moves you’ve ever made.
1. Efficiency and productivity
Machine control technology helps speed up earthworks processes, with the excavator or dozer operator following the job specification quickly and accurately from data supplied to them in-cab. Tasks are performed faster, with machine control eliminating the reliance on manual string-lines and pegs.
This leads to calculable savings in both project costs and task time, as faster completion of tasks translates into less fuel required for the job. Hardware can also be deployed in a more efficient manner, with plant where machine control is fitted being able to be pulled onto the next site faster.
Naturally labour costs across projects will drop too, with the workforce – specifically machine operators – being able to complete key tasks in a timely fashion with smarter tools to do the job.
All of this translates to tangible savings and a fast return on investment for companies investing in the technology.
2. Competitive advantage
Being able to give stakeholders the assuredness that accurate earth works operations will be completed in a timely manner, thanks to machine control, is a huge benefit during the tendering process. By also being able to carry out that work more effeciently than competition who may not be using the machine control technology translates purely to an increased ability to win deals.
Increasingly, as machine control becomes a standard part of the civil contractor’s ‘tool box’, client expectations will increasingly demand this technology be a component of successful tenders. This is already the case in some countries overseas, with New Zealand and Australia catching up quickly.
Potentially difficult environments or the requirement that work be completed within a small window of opportunity are no longer barriers to companies with limited machine resources or manpower. Machine control technology gives operators the ability to quickly and accurately follow plan data, as well as the flexibility to adjust quickly to any changes in specification.
Increasingly Kiwi companies are actively advertising their use of GPS machine control systems; the adoption of the technology is being seen by many as a billboard for their ability to innovate and stay ahead of the game.
Gallery
3. Safety
With its ability to eliminate the reliance on pegs and string-lines, machine control technology effectively removes a team member from the trench, as well as from within the working periphery of mobile plant.
This has an obvious benefit when it comes to on-site safety, with fewer team members being required to be working in the vicinity of heavy machinery.
4. Giving staff the tools to succeed
In the tight labour market we currently face, machine control technology gives newer team members the ability to step up to the challenge of complex site works immediately.
Machine control systems are intuitive to use and can be learnt quickly and competently. In fact machine control touchscreen interfaces are no more difficult to operate than the menu system in the average smartphone.
By having machine control on board, construction companies benefit immediately by being more attractive to potential employees who see the technology as part of the future of the industry.
5. The satisfaction of knowing the job is done right, first time
On the job, the operator knows where they are at and what their cut/fill is at all times. They can put the blade on the ground and know right to the millimetre how much further they have to cut or let the hydraulics on the blade take over, giving a perfect finish every time.
Chad Slater, Machine Control Manager for Synergy Positioning Systems, believes companies have the potential to save up to 15 or 20 percent on bottom line costs across a project with machine control systems utilised within the fleet. Synergy Positioning Systems is the New Zealand supplier of Topcon, the world’s largest distributor of machine control technologies.
“There’s an investment cost, naturally, but one decent job will pay for the technology and then there is also positive spin-offs from becoming known as a company that utilises machine control technology,” he says.
“These systems don’t reinvent the wheel, but they certainly make sure those wheels turn much more productively.”
More information on Topcon machine control systems, including real world case studies can be found on the Synergy Positioning Systems website, www.synergypositioning.co.nz. Alternatively, call Synergy Positioning Systems directly on 0800 867 266.
Back to all case studiesRelated Case Studies
-
Multi-Machine Control’s a Winner for BG Contracting
Progressive Christchurch construction firm BG Contracting takes on a wide variety of roading, drainage, general earthworks and surveying work. No two projects are quite the same, with a multitude of disciplines requiring various skills and ...
Read More -
Christchurch’s CCL Eliminates the Guesswork
CCL has been employing Topcon’s 3D Machine Control technology to not only provide accuracy in the field, but back up the bottom line in more ways than one....
Read More