News
- Topcon top of the pack for Finnish National Land Survey
- GPS Week Rollover
- A double win for Synergy at the Topcon Xperience Awards 2018!
- Topcon introduces new software for UAV inspection applications
- Topcon Talks About The Future of Construction in New Zealand
- International awards recognition for Synergy Positioning Systems
Newsletters
View all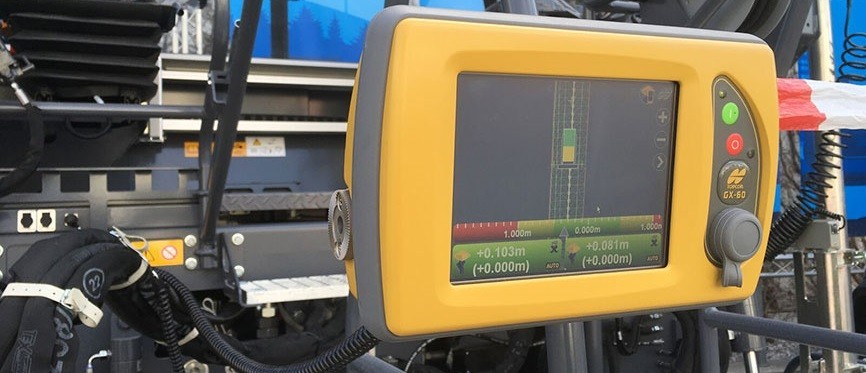
Topcon RD-MC offers the ultimate milling and paving solution
August 8, 2016 – Topcon has released the ultimate solution for large scale asphalt paving, ensuring speed and accuracy over long distances.
Synergy Positioning Systems remains at the forefront of technology solutions for the roading infrastructure industry, with the launch of new intelligent paving and milling technology from Topcon.
Following its debut at Bauma 2016 in Germany, Topcon’s RD-MC control system has now arrived in New Zealand.
Mike Milne, managing director of New Zealand Topcon distributor Synergy Positioning Systems, says the RD-MC system will help keep roading infrastructure entities productive and on-schedule during time-sensitive large-scale paving projects.
“The Topcon RD-MC system is probably the most comprehensive amalgamation of hardware and software solutions for mainline paving or milling projects that we’ve ever brought to market here.
“It essentially gives operators the ability to pave in 3D without the need for robotic total stations. This will prove especially beneficial for large-scale remedial work, where a 3D paving solution hasn’t until now been the most cost-effective way of working.”
Traditional 3D paving with multiple total stations remains an accurate solution, but line-of-sight to the paver is continually required so – if the surface to be paved is extensive – several robotic total stations are required.
“Especially where remedial work is required, this becomes expensive and time-consuming,” Milne continues.
“Instead of using robotic total stations, the RD-MC system uses GPS in conjunction with a sonic sensor to continually measure the pave depth. This way of working comes into its own when the project calls for a mill-and-fill approach, as the RD-MC system accurately compensates for an uneven sub-surface and differential compaction.”
The system allows road crews to load a 3D design into the RD-MC system, complete a pick-up of the existing surface and then lay new asphalt precisely to specification thickness along lengthy stretches of road or runway.
Operations personnel can simply ride along and monitor progress as the Topcon control system ensures the paver automatically responds in real-time, accounting for every surface change so as to deliver a smooth, finished surface.
The Topcon RD-MC (Real Dimensional Machine Control) system works by utilising the processing power of four key elements; an ST-3 Sonic Tracker which delivers real-time vertical measurements using advanced digital signal processing; an MC-R3 GNSS (Global Navigational Satellite System) receiver which is interchangeable with integrated GNSS, radio and controller to receive RTK corrections; an MC-G3 GNSS antenna to capture available GNSS satellite data; and a ruggedised GX-60 control box and touchscreen display from where the operator controls either the milling machine or the paver.
“This is the sort of technology that will change the way milling and paving crews work in a variety of scenarios,” concludes Milne.
“Using a hybrid approach with several solutions rolled into one, the Topcon RD-MC control system will save roading contractors time, reduce the amount of equipment required and allow crews to accurately achieve the high level rideability specification desired by regulatory authorities, even on the most demanding rehabilitation projects.”
For more information on the Topcon SmoothRide Resurfacing click here.
For more information on Topcon’s range of specialised 3D machine control systems and back-end software solutions, click the contact us button:
Back to news listings