News
- Topcon top of the pack for Finnish National Land Survey
- GPS Week Rollover
- A double win for Synergy at the Topcon Xperience Awards 2018!
- Topcon introduces new software for UAV inspection applications
- Topcon Talks About The Future of Construction in New Zealand
- International awards recognition for Synergy Positioning Systems
Newsletters
View all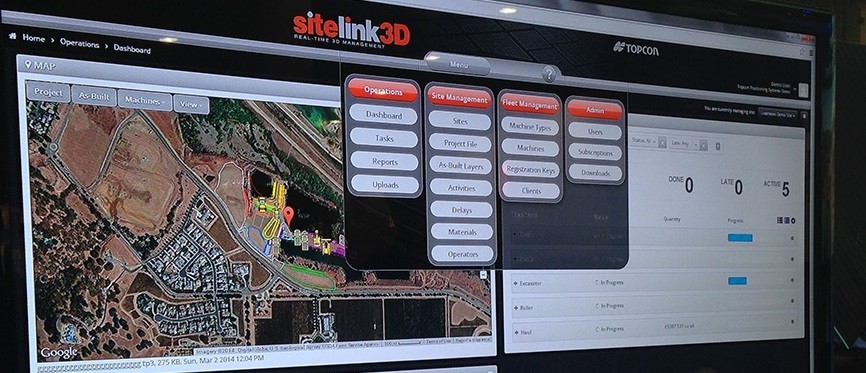
Topcon Enterprise Site Management Solutions Explained
July 8, 2015 – Enterprise solution for complete site management
|
Machine automation based on highly accurate positioning and smooth data transfer, has become a major tool to increase performance and profitability of individual machines on a construction jobsite. When connecting multiple machines via telemetry, and back to an office or site control center, we now have many new possibilities to automate and manage a complete workflow, instead of single machines only.A site management system connects all parts of a construction site together – people, data, devices, machines with calculating, scheduling and controlling. It’s the one system that provides construction companies with a way to manage their projects and resources effectively. It provides communication, planning, management and collaboration tools that shows real-time site status and improves estimation , execution and controlling. Sitelink3DThe Sitelink3D platform offers multiple levels of connectivity on site and back to the office, and even allows the user to create tasks, and monitor the construction progress in real time. At the heart of the system is the Sitelink3D cloud server that manages all connectivity on site via reliable and secure connections. New or updated job design files are easily shared, and remote support or troubleshooting of machines can be carried out from behind the desk. A chat-function offers instant communication to or between operators, all connected machines can easily work from different references in the same design, and view each other’s progress as the work progresses. In cases where cloud access is not available, local communication networks can be set up. Via the new Sitelink3D Enterprise module, the possibility to create tasks and dispatch them to the machine/operator is now available. For each machine, target timelines, quantities and areas can be defined and combined in individual tasks. As the system tracks real time as-built surfaces, a continuous and historical overview is available of progress made. The system constantly measures site progress through volumetric monitoring, and is able to present this in reference to the individual tasks. Unique progress reports that present as-built versus schedule give the site manager dedicated coaching possibilities and improve the overall end-result. Siteview even allows you to view in real time all machines as they perform the work. The task creation has the possibility to include haul truck earthmoving activities as well. By connecting your dumpers, continuous progress is kept of volumetric mass haul movements, and incorporated in the integrated work progress reports. DynaRoad – mass haulOn larger jobs, the planning already kicks in at an earlier stage, either as a basis for a bid process or for overall planning and job work planning purposes. This is way before even communication, like Sitelink3D, is in place. For the planning DynaRoad brings advanced project scheduling solution for owners, contractors and designers, to optimize scheduling and production control of large, complicated earthmoving projects. DynaRoad takes every project in three parts; planning, scheduling and controlling. The planning module optimizes design based mass haul, takes various cost and distance parameters into account, as well as cut and fill balance. The planning is available per construction zone division and data can be imported and exported for further processing. The scheduling module allows connection to the mass haul planning with resources, quantities and locations and creates powerful time-location maps, as well as Gantt views and resource graphs. The control module reports the progress while the job is being executed. It allows control actual versus budgeted production rates, mass hauls and remaining cut and fill. This is a true connection between work performed and original plans, schedules and budgets. DynaRoad offers the most advanced in map based production planning, to manage cut and fill operations, and keep an overview of production and progress during construction. Integrated Site managementIndividually automated machines now offer the possibility of interconnectivity, with additional people and devices on site, allowing for real time as-built tracking. Based on this, progress, performance and productivity becomes available during construction, closing the loop to plans and budgets. Sitelink3D: It’s the link that combines the best out of all those into one product that challenges the entire job site process or any part you choose of it. For more information about Site Link3D, click the contact us button: |