News
- Topcon top of the pack for Finnish National Land Survey
- GPS Week Rollover
- A double win for Synergy at the Topcon Xperience Awards 2018!
- Topcon introduces new software for UAV inspection applications
- Topcon Talks About The Future of Construction in New Zealand
- International awards recognition for Synergy Positioning Systems
Newsletters
View all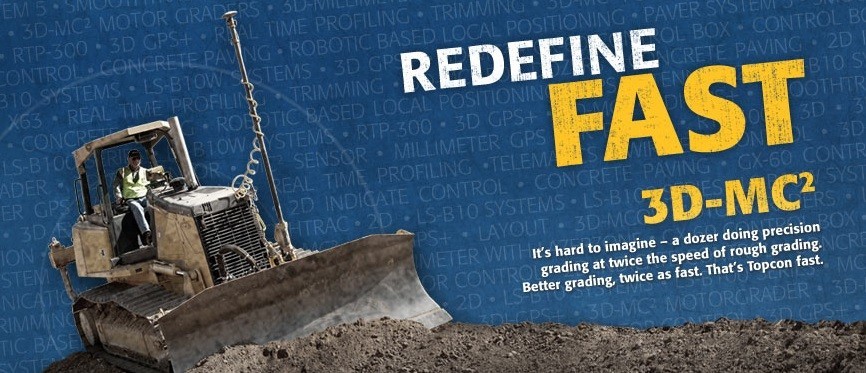
Machine Control Revolutionises The Industry
Not only is machine control technology ensuring faster, safer and more accurate work for contractors, it’s saving companies money too.
|
May 2014 – Topcon’s machine control technology effectively ensures every project is a stakeless project, incorporating satellite positioning and digital 3D modelling so dozer, grader and excavator operators can see where they are on any site in real-time. The resultant cut/fill information appears right there on the screen in the cab instantaneously and consistently, meaning that every operator has all the information they need right at their fingertips, and without the need for stakes. Chad Slater, Synergy Positioning System’s Machine Control Manager, who has many years experience working with Topcon machine control systems on large scale construction projects in his native Canada, says that companies adopting such systems stand to make substantial gains in the long run. |
|
![]() |
But it isn’t just time that machine control technology saves. The system means that downtime is kept to a minimum, with the instances of the operator over-cutting (and then having to back fill) completely eradicated. That means a company will require less manpower on site and won’t need to halt operations while surveyors are called in to re-stake; all adding up to cost savings across the length of a project. |
|
|
Chad says that machine control technology has gotten so accurate; many overseas contractors are using dozers running machine control systems to complete the sort of finishing work a motor grader might usually be tasked with. Topcon’s 3D-MC² sensor tracks and predicts blade movement in every direction, making cut adjustments much faster than any other GPS-based system.
|
|
![]() |
There are specialised Topcon systems for dozers, motor graders, excavators, scrapers and compactors. Find out more information about the extensive Topcon range at www.synergypositioning.co.nz or get in touch with one of Synergy Positioning’s machine control experts on 0800 TOP CON. |